The Comprehensive Guide to Injection Plastic Molding
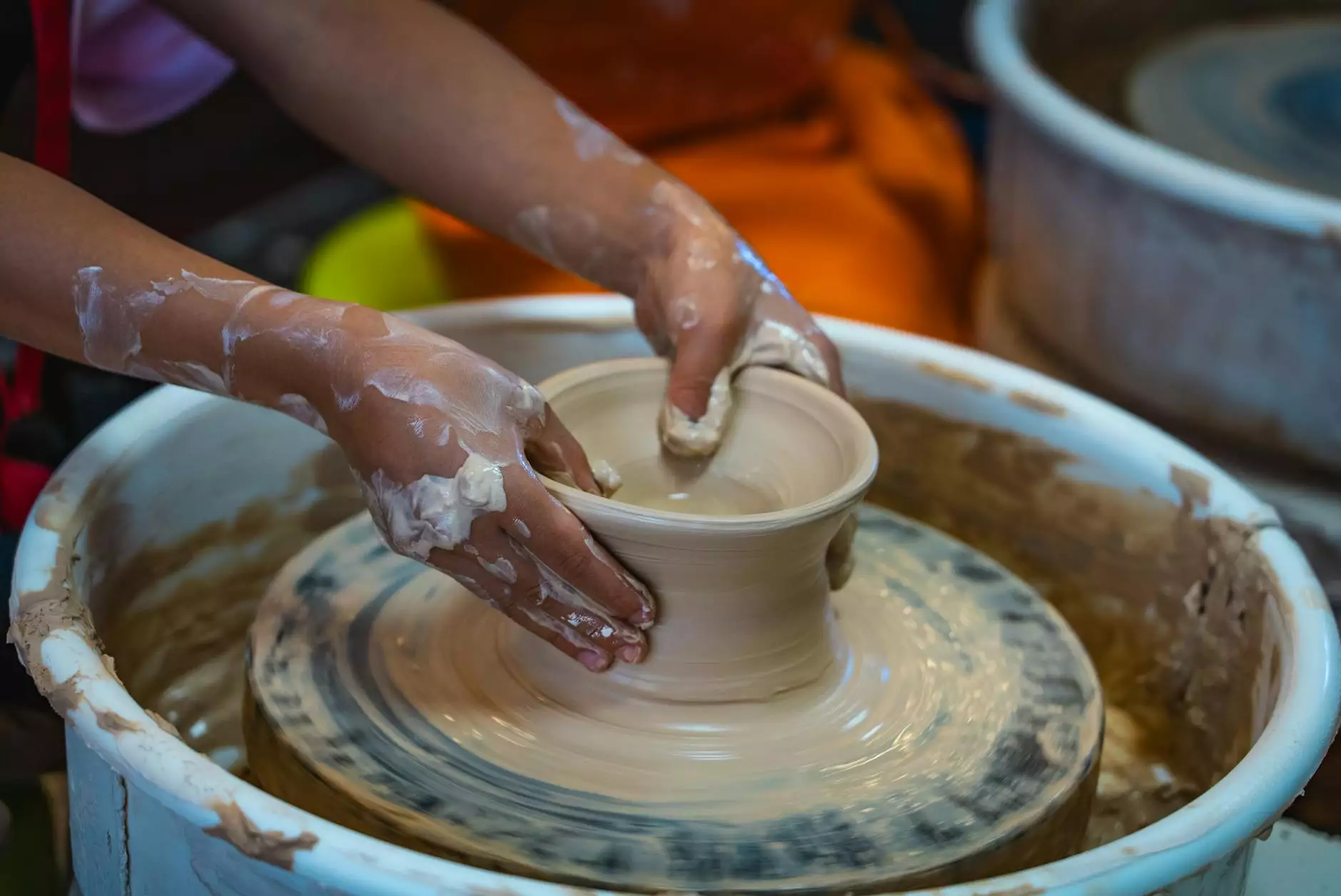
In the ever-evolving world of manufacturing, injection plastic molding stands as a cornerstone of modern production techniques. This method is revered for its efficiency, versatility, and ability to produce complex shapes with precision. In this article, we will delve into the intricacies of this process, exploring its benefits, applications, and the significant role it plays in various industries, particularly as showcased by leaders like Deep Mould.
What is Injection Plastic Molding?
Injection plastic molding is a manufacturing process used to produce parts by injecting molten material into a mold. The process is particularly popular for creating plastic parts, but it can also be used with other materials such as metals and glass.
The Process of Injection Molding
The injection molding process involves several key steps:
- Material Preparation: Raw plastic pellets are fed into a hopper, where they are heated until they melt.
- Injection: The molten plastic is injected into a mold at high pressure.
- Cooling: The injected plastic is allowed to cool and solidify within the mold.
- Demolding: Once cooled, the mold opens, and the finished part is ejected.
Types of Injection Molding
There are various types of injection molding processes, including:
- Continuous Injection Molding: Used for producing long runs of identical parts.
- Batch Injection Molding: Ideal for smaller production runs, allowing quick changes in molds.
- Gas-Assisted Injection Molding: Incorporates gas to create hollow sections, reducing material use and weight.
- Thermal Injection Molding: Involves the incorporation of heat to accelerate cooling rates.
Benefits of Injection Plastic Molding
The popularity of injection plastic molding can be attributed to its numerous advantages, such as:
- High Efficiency: The process allows for the rapid production of high volumes of parts, significantly reducing manufacturing time.
- Material Versatility: A wide range of materials can be used, including thermoplastics, thermosetting polymers, and even bioplastics.
- Precision and Repeatability: Injection molding produces parts that meet tight tolerances, ensuring quality and consistency.
- Complex Geometries: The process can create intricate designs that are often impossible or costly to manufacture using other methods.
- Minimal Waste: The controlled process results in less scrap material compared to traditional machining methods.
Applications of Injection Plastic Molding
Injection molding is used across various industries, making it an integral part of modern manufacturing. Some notable applications include:
- Automotive Industry: Production of components such as dashboards, panels, and connectors.
- Consumer Electronics: Used for creating housings, buttons, and connectors for devices.
- Medical Devices: Essential for manufacturing precision parts like syringes, inhalers, and surgical instruments.
- Packaging: Widely used for producing bottles, containers, and packaging materials.
- Toys: The manufacturing of complex parts that make toys functional and aesthetically pleasing.
Case Study: Successful Applications in the Automotive Sector
In the automotive industry, injection plastic molding processes have been employed to revolutionize component production. Companies like Deep Mould have led efforts to innovate in this field by ensuring high standards and efficient production lines that reduce time-to-market.
Some examples of successful applications include:
- Instrument Panels: Currently being produced through injection molding, allowing for intricate designs and easier assembly.
- Exterior Trim: Offers a clean finish, essential for consumer appeal.
- Lightweight Structural Components: Important for improving fuel efficiency without compromising safety.
Challenges in Injection Plastic Molding
While injection plastic molding is a highly efficient manufacturing method, it is not without its challenges. Some challenges faced by manufacturers include:
- Initial Setup Costs: The costs for molds and machinery can be high, making it less accessible for small-scale operations.
- Material Constraints: Not all materials can be easily molded, and some may require special considerations.
- Production Breakdowns: Machine malfunctions can result in lower output and increased costs.
- Environmental Concerns: As with all plastic manufacturing processes, there are issues related to waste management and recycling.
Future Trends in Injection Plastic Molding
The future of injection plastic molding looks promising, with several trends poised to influence the industry:
- Sustainability Efforts: The shift towards sustainable materials, including bioplastics and recycled plastics, is set to gain momentum.
- Smart Manufacturing: The integration of IoT technologies in the production process will enhance efficiency and quality control.
- Automation: The increasing use of robotics to handle complex operations can reduce labor costs and increase precision.
- Customization: Advances in technology will allow for more tailored solutions to meet consumer demands.
Conclusion
Injection plastic molding remains a vital process in the landscape of modern manufacturing, delivering unmatched benefits across various sectors. Companies like Deep Mould continue to set the standard for quality and efficiency in this industry, emphasizing the significance of innovation. As we look ahead, embracing the challenges and advancements in this field will be crucial for sustaining its transformative power in both established and emerging markets.
By understanding the nuances of injection molding, businesses can better position themselves to leverage this technology, ensuring they remain competitive in an increasingly demanding marketplace.